Disk/Blade Dovetail Connection
Sample Applications
Disk/Blade Dovetail Connection
Thermo-mechanical fatigue and time dependent crack growth analysis
Metal alloys are continuously being improved to provide greater strength against component failure and also to increase resistance against crack propagation. This is a particular issue in nickel based alloys used in aerospace engines which experience high temperatures under both sustained and cyclic loading conditions. Traditional analysis techniques account for fatigue crack growth effects but time dependent crack growth is generally more difficult to evaluate. The "full cycle" capability in Zencrack is demonstrated in this example which shows combined fatigue and time dependent crack growth prediction in a cracked disk.
The proprietary nature of aerospace engine components and material data means that "real" geometry and material data must be replaced with "representative" data. For the purposes of this example, a simplified model is defined with key data based on several publications:
- Ref. 1 - Geometry of disk and blade
- Ref. 2 - Spatial variation of peak temperatures
- Ref. 3,4 - Time variation of rotation speed and temperatures
- Ref. 5 - Temperature dependent material data, Walker and COMET crack growth data
The geometry used for the analysis is a single sector of the disk shown in Figure 1. Two contact regions are defined for the blade/disk interaction. Examples of references of spatial temperature variation and engine speed through a flight cycle are shown in Figure 2. These have been used to develop the spatial and time history loading variations used for the analysis. Figure 3 shows the simplified flight cycle consisting of take-off and climb, cruise, descent and landing. The peak temperature occurs shortly after the peak engine speed at the end of the climb phase.
The key features used in the analysis include:
- Temperature dependent Young's modulus and Poisson ratio
- Fatigue crack growth data with temperature dependency (Walker equation)
- Time dependent crack growth data with temperature dependency (COMET equation)
- Modelling of the time history of temperature and engine speed for one flight cycle in the finite element analysis
- Extraction of results of the flight cycle analysis into a "full cycle" load history for input to crack growth calculations
- Handling of different temperatures at the Kmax and Kmin conditions when calculating da/dn
For the simplified flight cycle used in the analysis there is only one fatigue cycle per flight cycle - the major cycle. If a more detailed time history was used, the analysis is optionally able to extract minor cycle information from the results of the finite element analysis.
Analysis results for a corner crack position are shown in Figure 4. This demonstrates that the inclusion of time dependent crack growth in the analysis reduces the predicted life, in this example by about one third.
Additional information about the analysis, animations of some of the results and some of the detailed flight cycle outputs that can be extracted are shown in the video in Figure 5.
Figure 1 - Single sector of the uncracked component with contact surfaces highlighted
Figure 2 - References for spatial temperature data [2] and typical engine speeds [3]
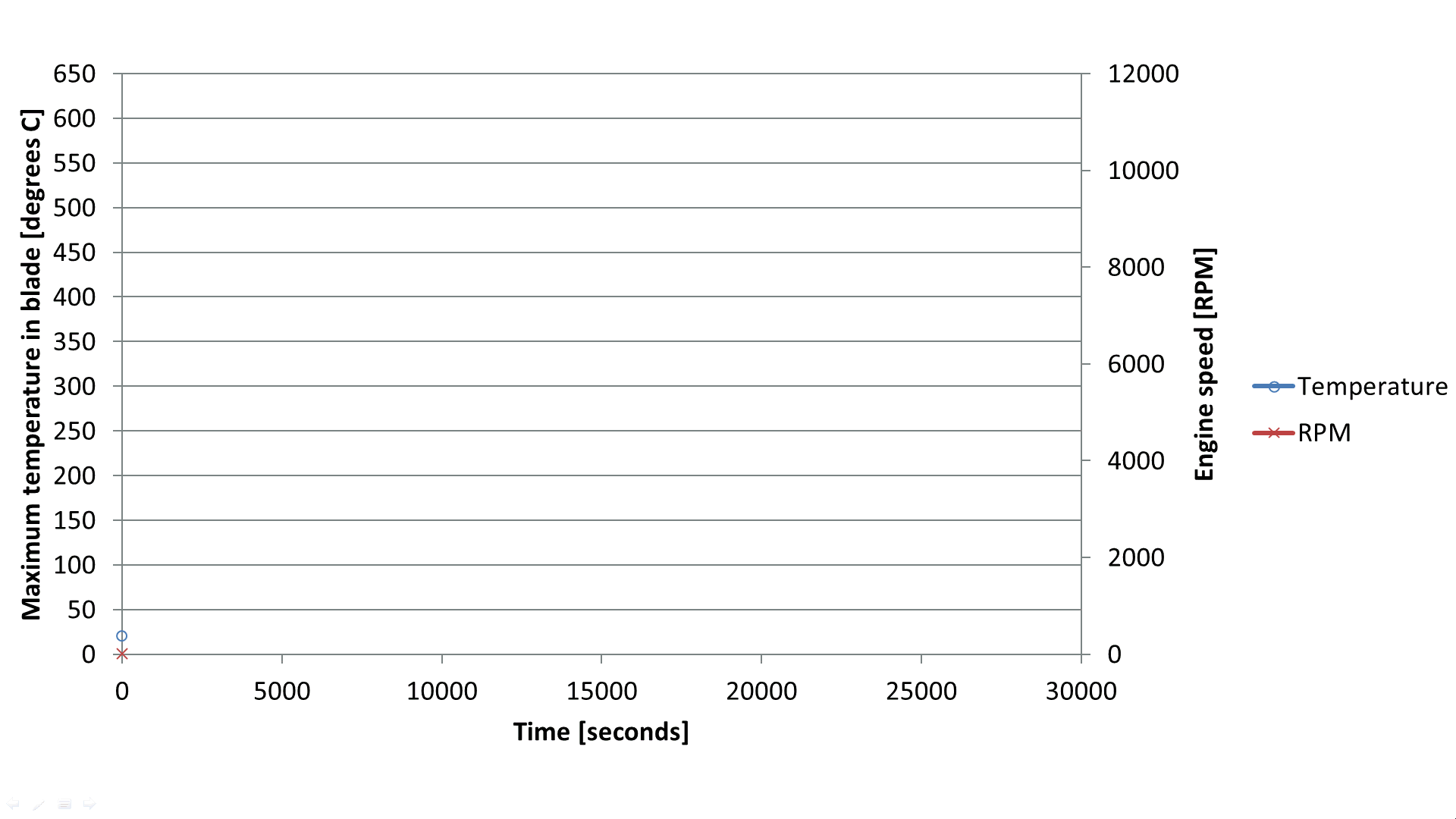
Figure 3 - Time history of engine speed and maximum temperature
Figure 4 - Reduction of life for combined fatigue and time analysis compared to fatigue-only analysis (corner crack)
References
1. Methodology for Structural Integrity Analysis of Gas Turbine Blades, de Oliveira Vale et al, J. Aerosp. Technol. Manag., Vol. 4, No. 1, pp. 51-59, Jan.-Mar. 2012.
2. Failure Analysis of Turbine Disc of an Aero Engine, Witek, Engineering Failure Analysis, 13 (2006) 9-17.
3. Gas Turbine Disk-Blade Attachment Crack, Davidson, Journal of Failure Analysis and Prevention (2005) 1:55-71.
4. The Fatigue Behavior of Small Cracks in Aircraft Turbine Disk Alloys, Romanoski, PhD Thesis, MIT, Feb. 1990.
5. Zencrack 7.8 Examples Manual, Example ex07, Zentech International Limited, 2012.