- R&D
Projects
Projects
Find out about some of the R&D projects in which Zentech has participated and some of the areas of expertise available via our links with Brunel University London.
TSB Project
A Technology Strategy Board UK Government-funded development called DISPLACE was aimed at 'technology to increase the life & reliability of advanced lightweight Ni-based gas turbine discs'. Led by Rolls-Royce plc, participants included industry and academia:
- Rolls-Royce plc (Derby)
- Serco
- Zentech International Limited
- Birmingham University
- Portsmouth University
“The work carried out by Zentech for this project will provide new and enhanced capabilities within the Zencrack software. A significant enhancement will be made to the combined fatigue and time dependent analysis capability for full flight cycle analysis. This includes enhancement in the options for time dependent crack growth laws and the addition of an option for including the effect of minor cycles during the fatigue crack growth calculations. The complex interaction between stress and temperature time histories is treated in a thorough manner with industry-standard options included to define the method of association of temperature with fatigue cycles during evaluation of crack growth rates. Although the framework of this project addresses a specific aerospace requirement, the capabilities introduced in Zencrack are general and can be applied to other industry areas where thermo-mechanical fatigue and high temperature crack growth present significant problems. ”
Reference: TP/8/MAT/6/I/Q1525K.
SBIR Project
A SBIR funded project with the Air Force Research Laboratory at Wright Patterson Air Force Base, Dayton, Ohio, USA was aimed at enhancing existing crack simulation capabilites in Zencrack.
“The objective of this SBIR was to incorporate new features in the fracture mechanics software, Zencrack, including cyclic and time-dependent load spectra, residual stress distributions, generalized Willenborg retardation, user-defined crack fronts (e.g. for transition from semi-elliptic to through cracks) and automatic large 3-D crack growth. Zencrack was also interfaced to ANSYS in addition to enhanced interfaces to ABAQUS and MSC.MARC. Zencrack models crack fronts by replacing solid elements in finite element (FE) meshes by detailed regions of crack-blocks. The CTOD method was added to the existing 3-D J-integral facility to compute stress intensity factors (SIF) and direction of crack propagation under mixed mode LEFM loading. Numerical crack growth integration algorithms were developed for superposition load systems (e.g. static residual stresses and cyclic loading). New 3-D meshing features to minimize element distortion were developed including large crack-blocks with transition elements at crack block tied surfaces, mesh ‘relaxation’, crack-block boundary shifting and boundary flipping of through cracks. Fatigue and time-dependent crack growth data can now be specified as a function of stress ratio and temperature using Paris Law segment data, tabular data or in a Zencrack user subroutine. Validation of the software was conducted by benchmarking against AFGROW software, data and theoretical solutions.”
Reference: AFRL-ML-WP-TR-2004-4014.
Sample projects conducted by our associate consultants at Brunel University London
Through our close collaboration with many academics at Brunel University London, we have developed a wealth of expertise and capabilities in advanced numerical modelling.
Development of shell and solid-shell finite elements
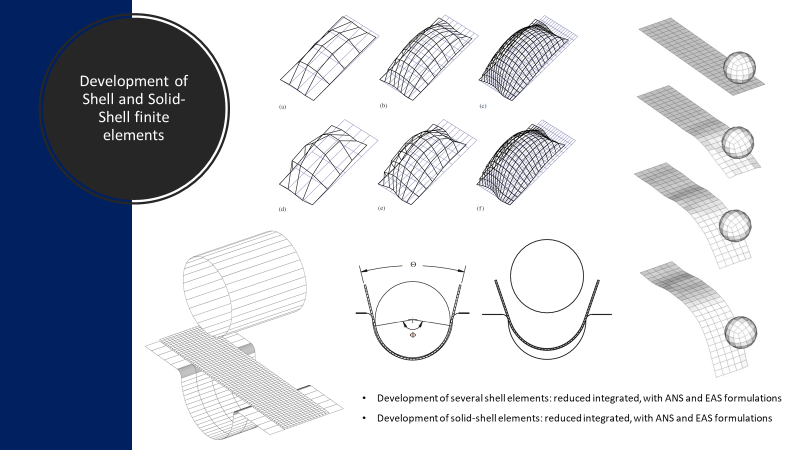
Highly non-linear contact and self-contact analysis
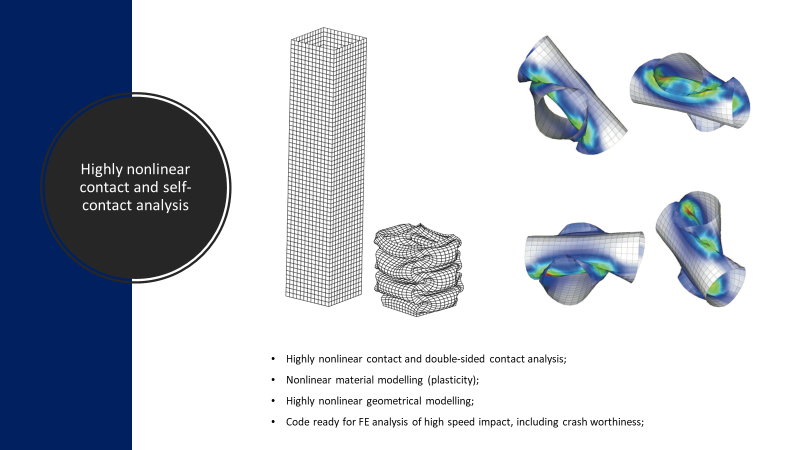
Thermo-mechanical analysis for steel structures under fire
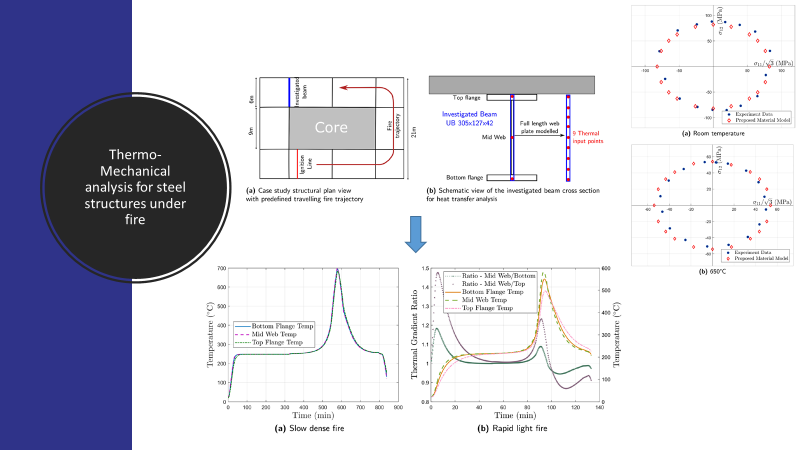
Meshless methods for fluid flow
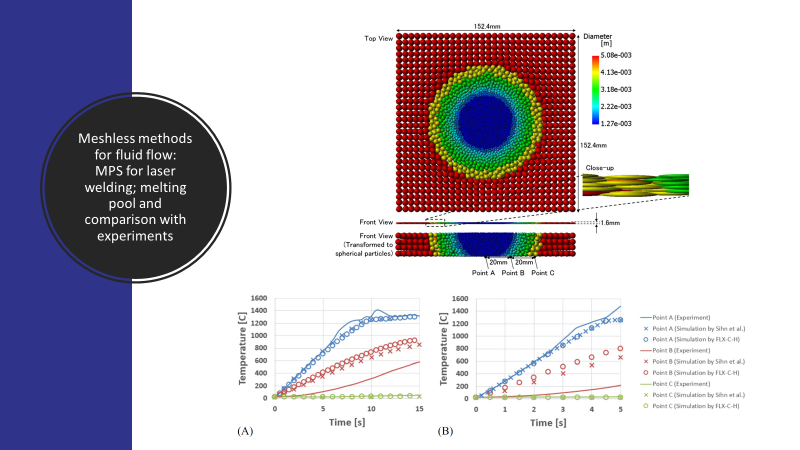
Helicopter crashworthiness on water
Fluid-structure interaction is extremely challenging to simulate due to non-linearities (geometric, material and contact) and prediction of structural collapse for thin-walled structures with plasticity, damage and failure. In addition, the water model has to allow for cavitation and formation of shockwaves.
Fixed wing aircraft ditching
The main challenge for contact algorithms in this type of simulation is ingress of water after the structural failure. These challenges have been successfully addressed in modelling of helicopter and fixed wing aircraft ditching using transient non-linear finite element method coupled with smoothed particle hydrodynamics (SPH).
The same approach was used was used in the modelling of bird strike on fan blades and fuel sloshing.
Numerical methods
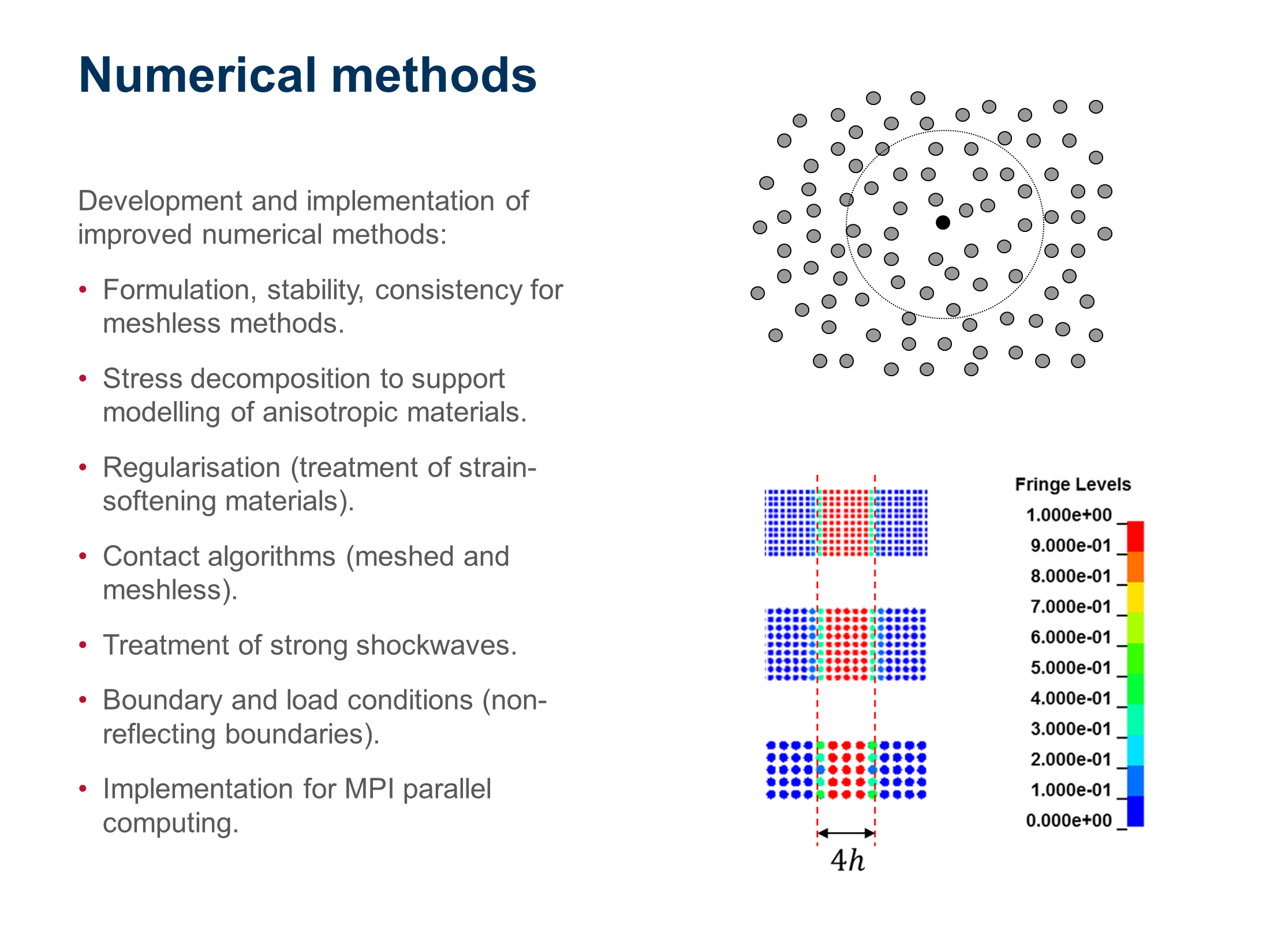
Material behaviour
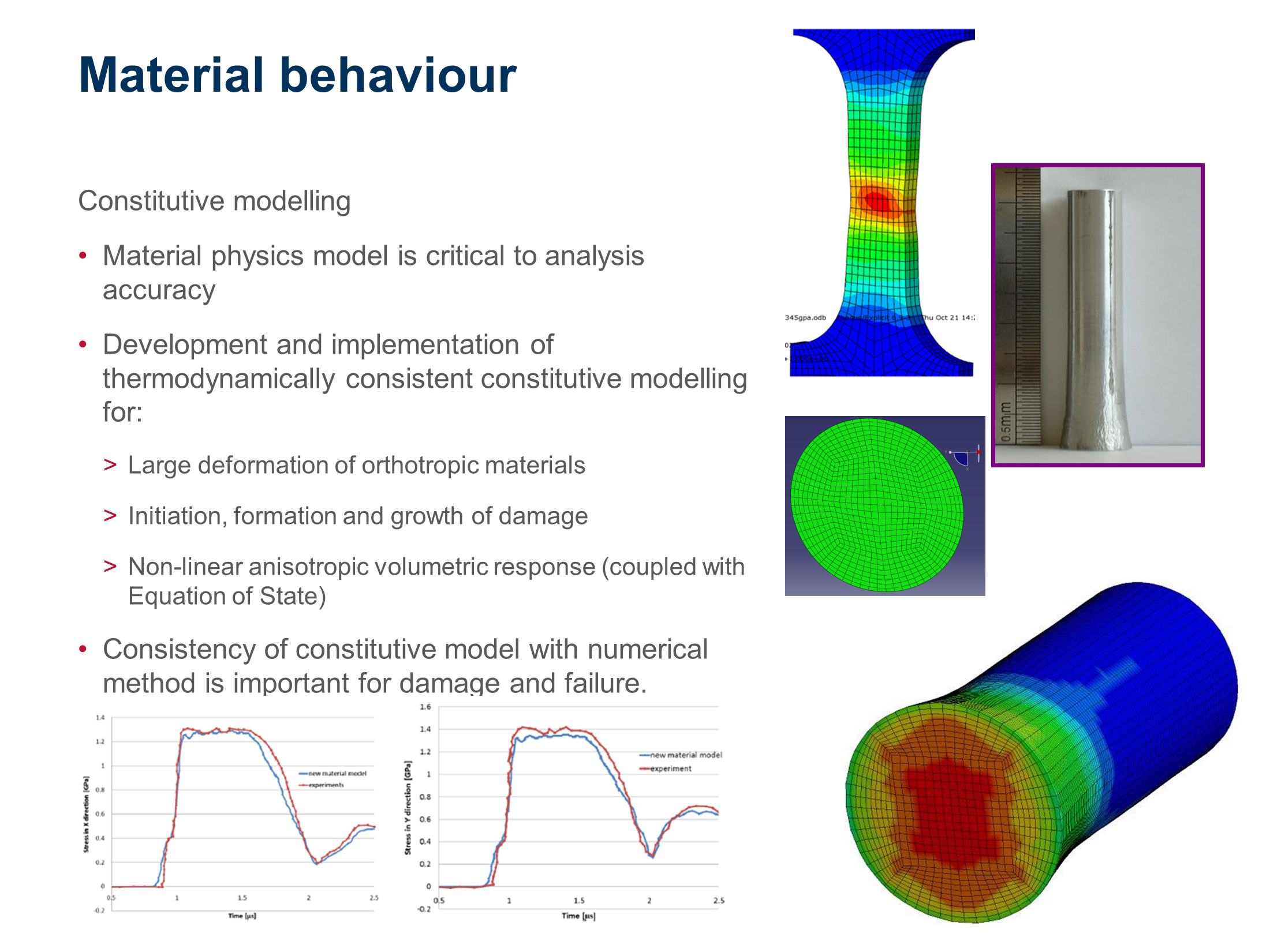
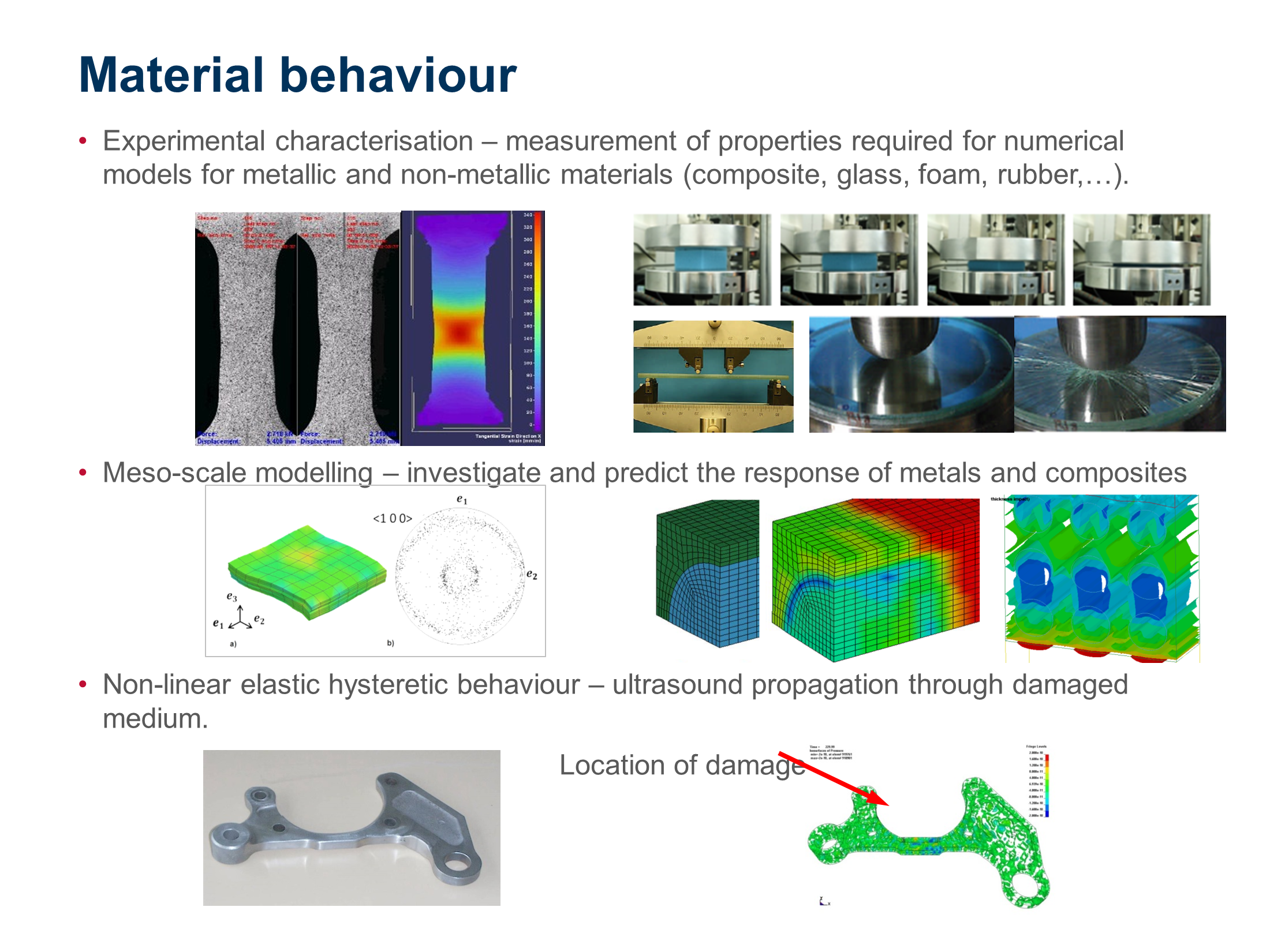
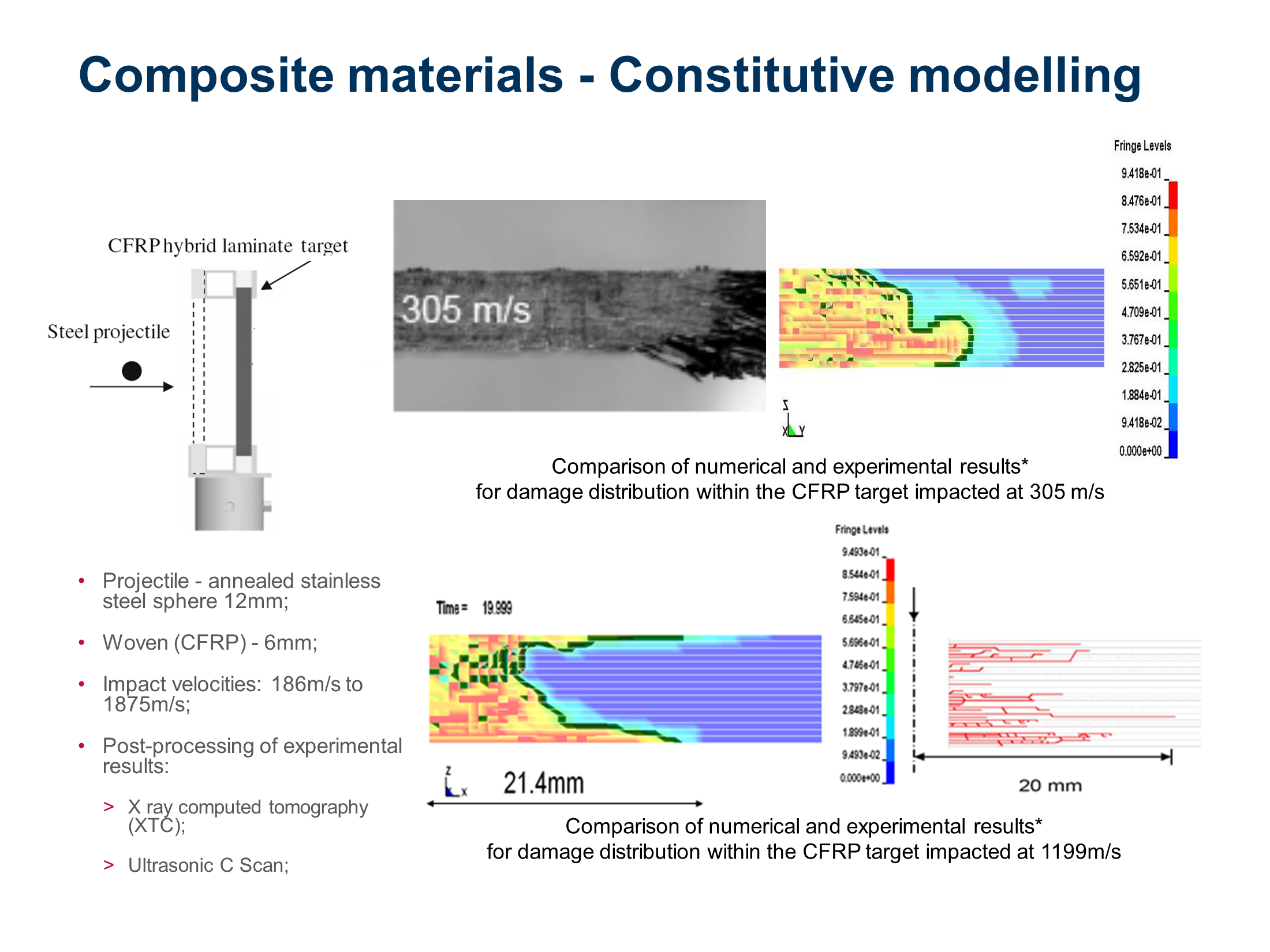
X-ray computed tomography in material fracture characterisation
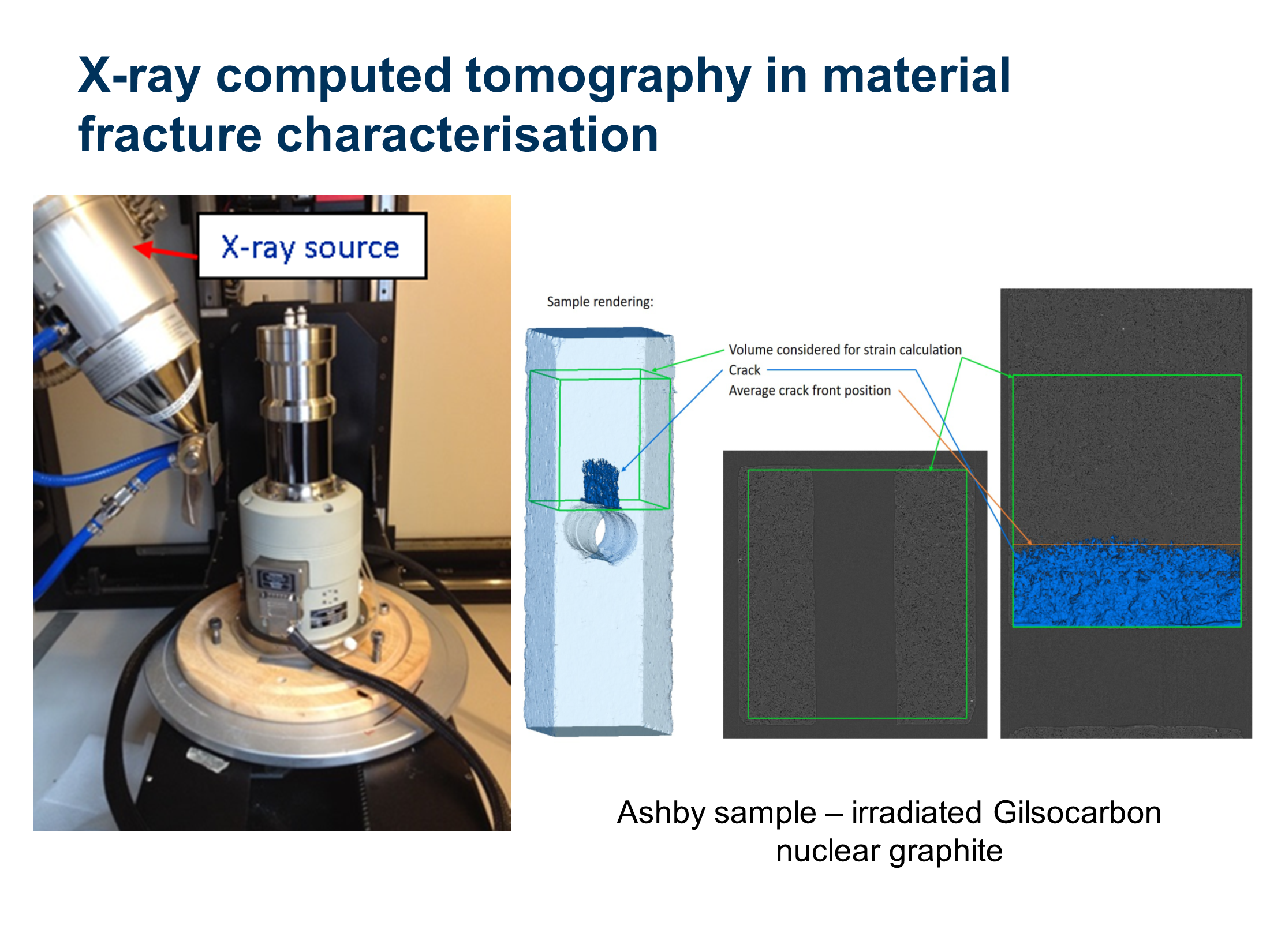
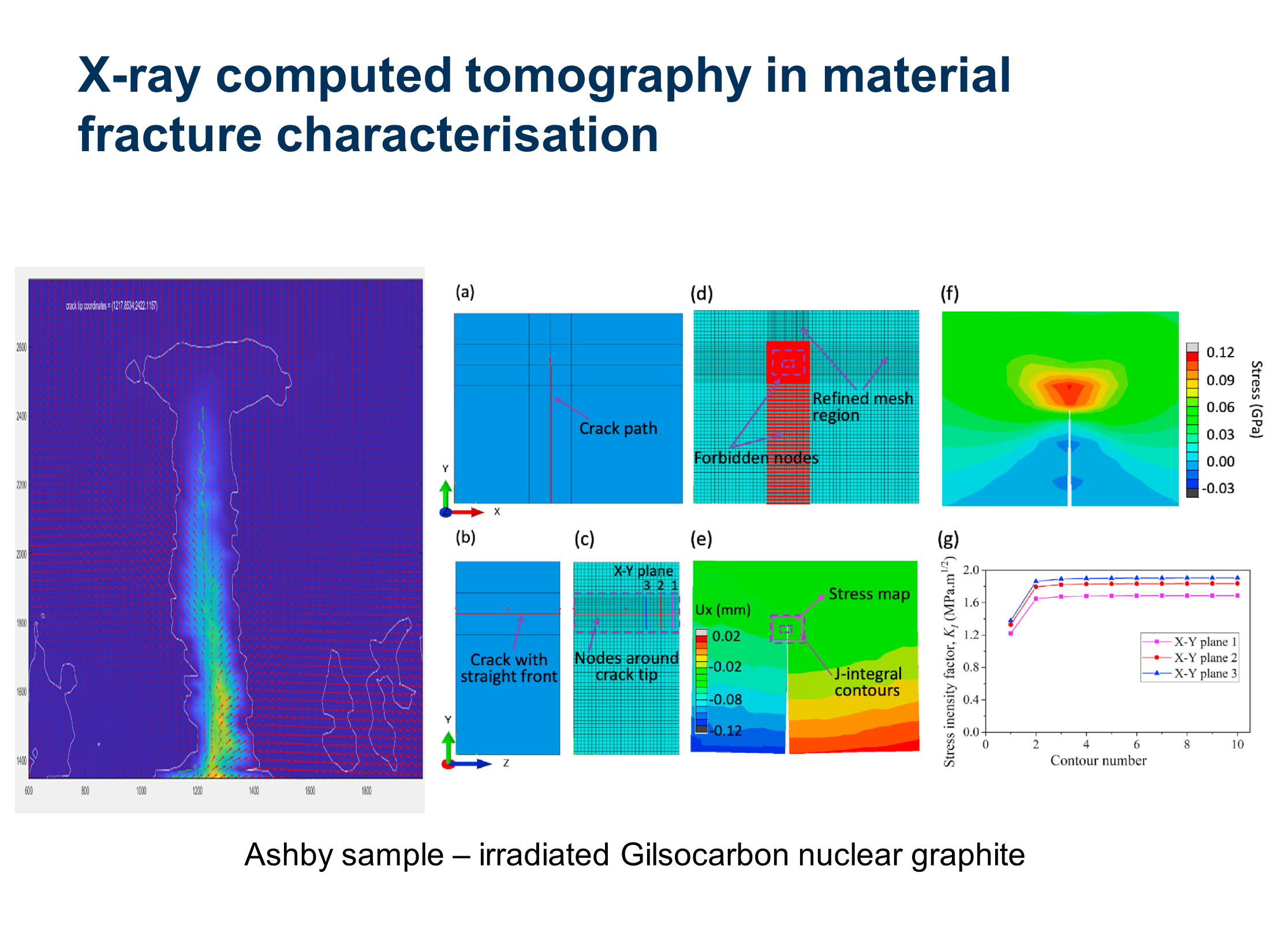
Ultimate load prediction
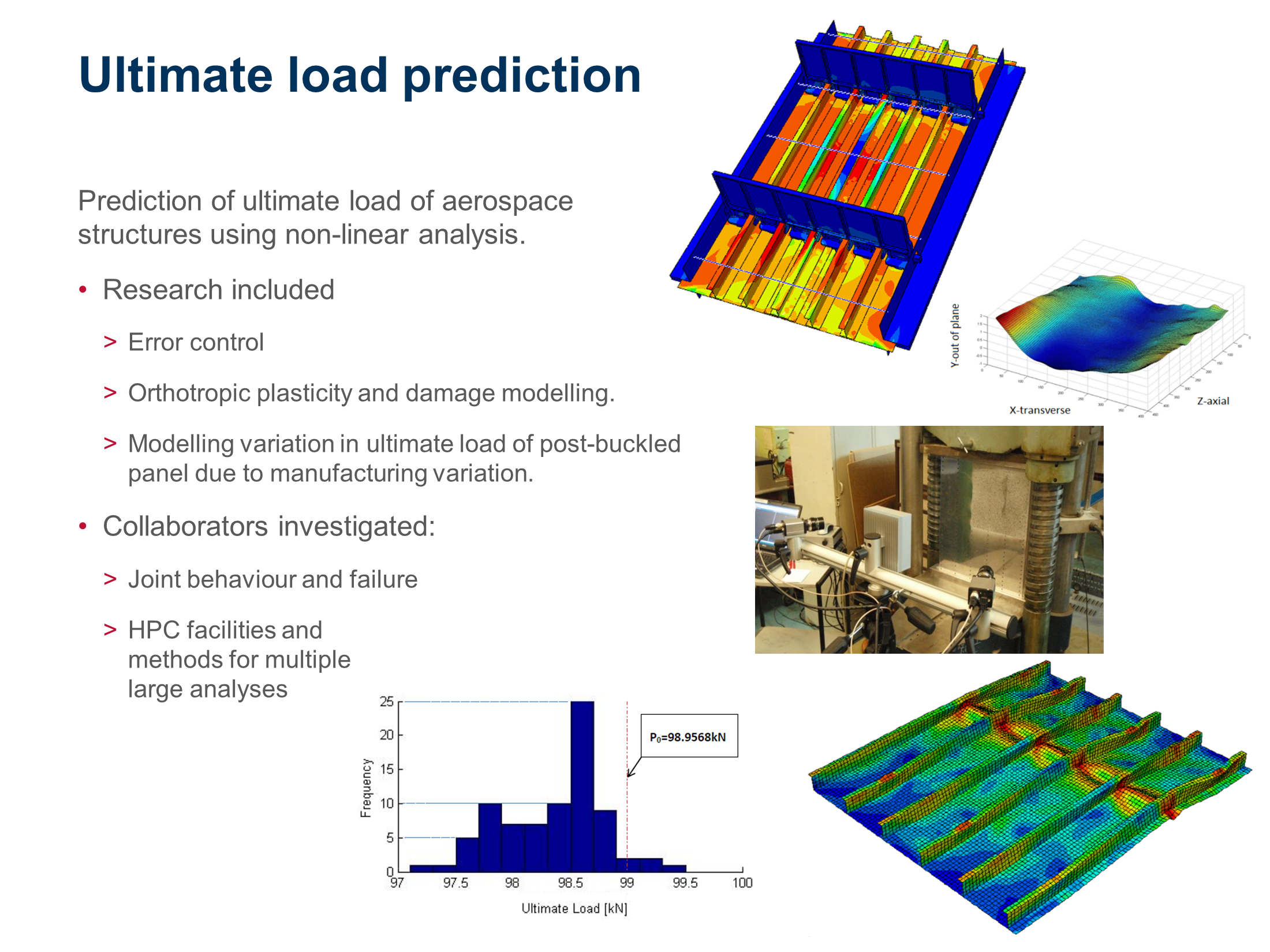
Friction stir weld modelling
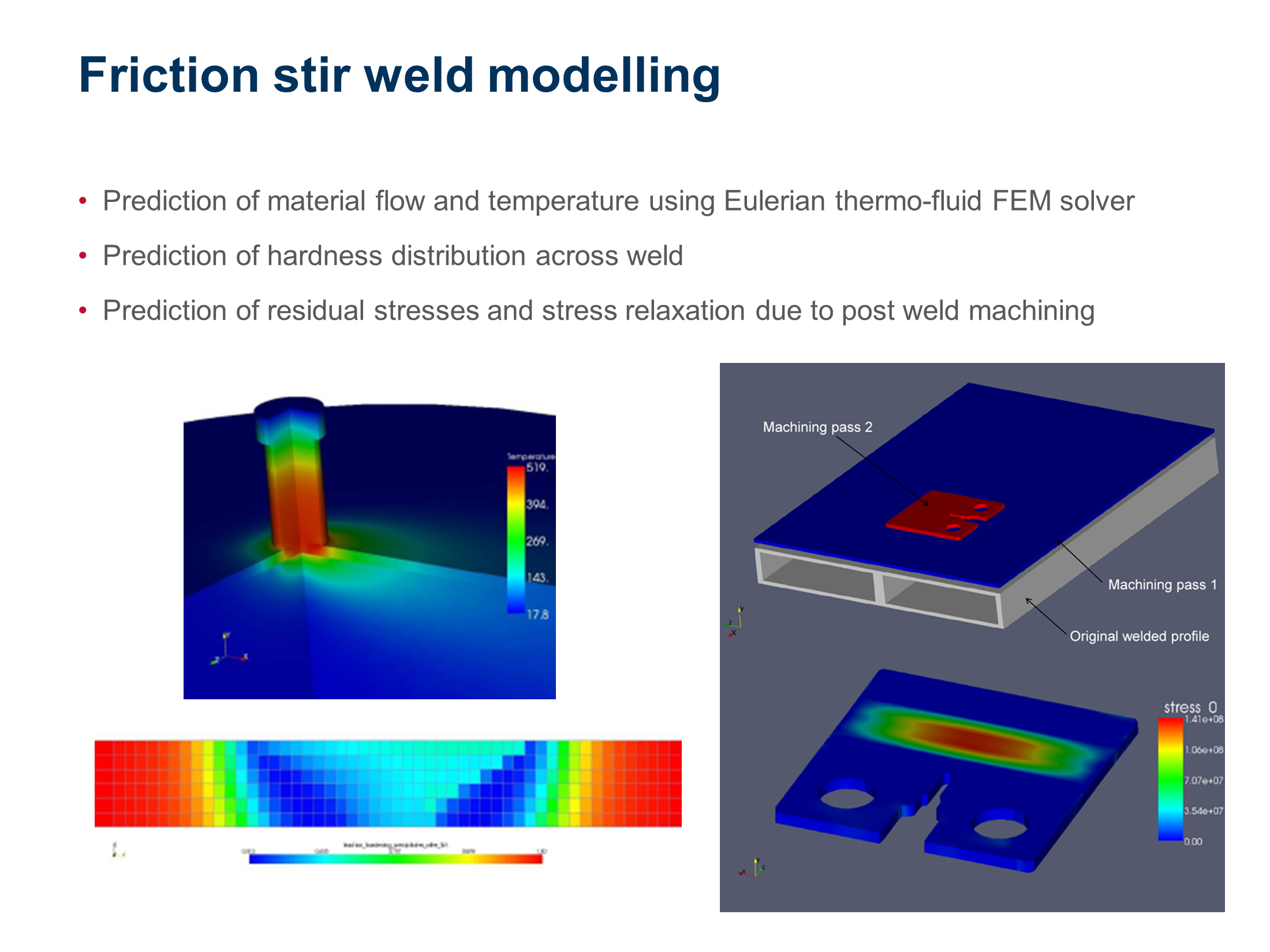
Analysis of extreme loading
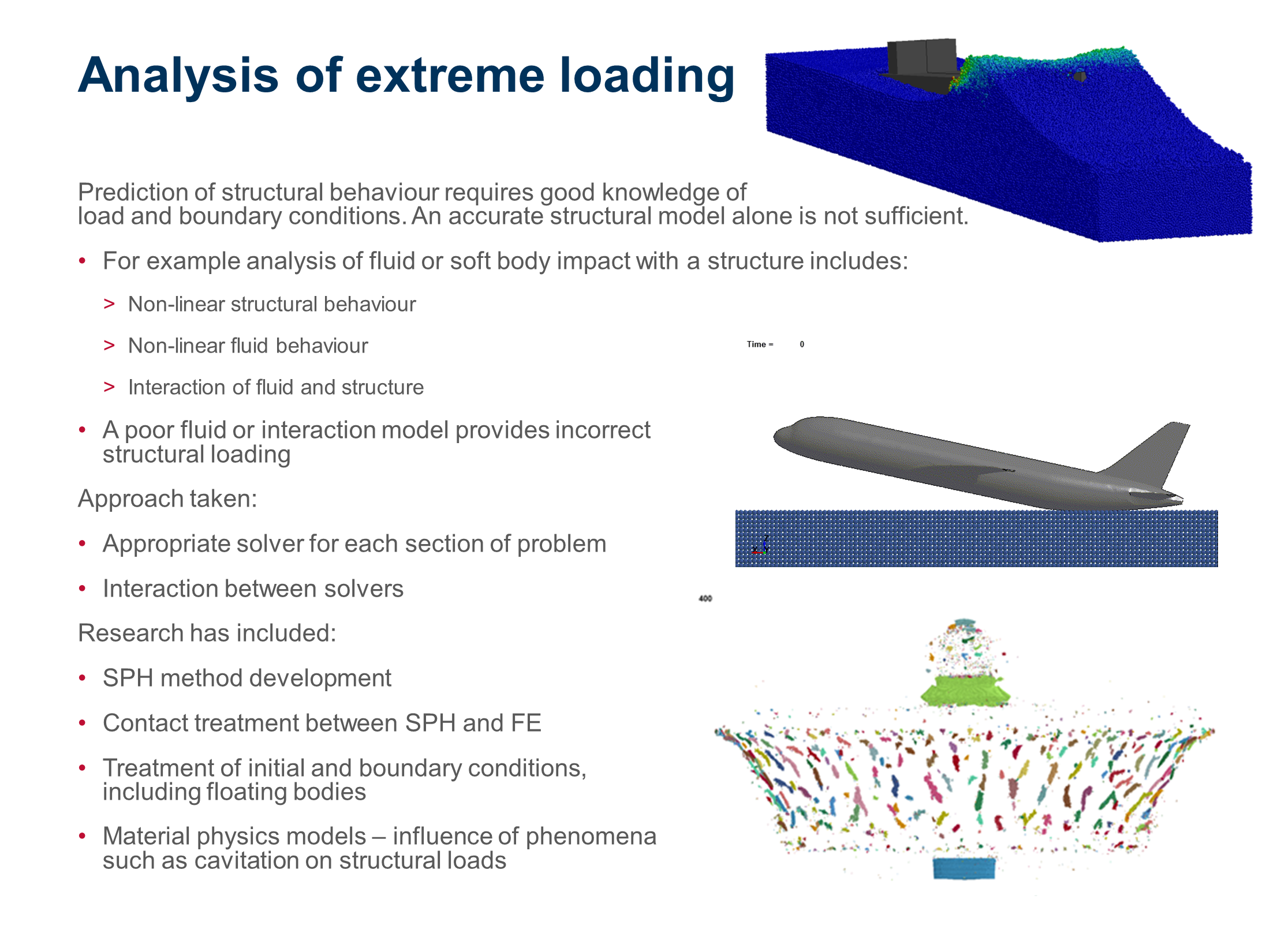
Fragmentation and explosive loading
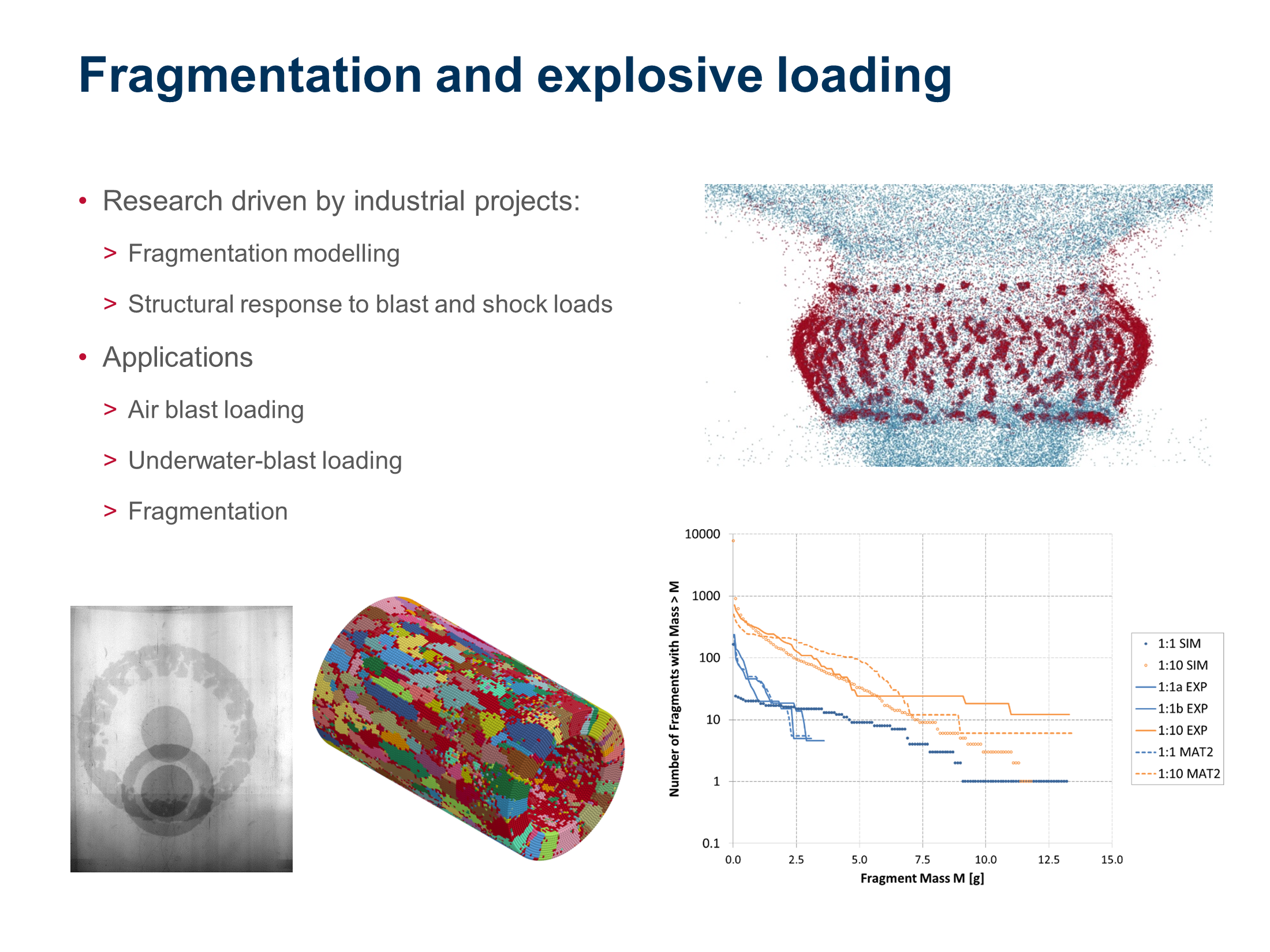
Impact validation tests
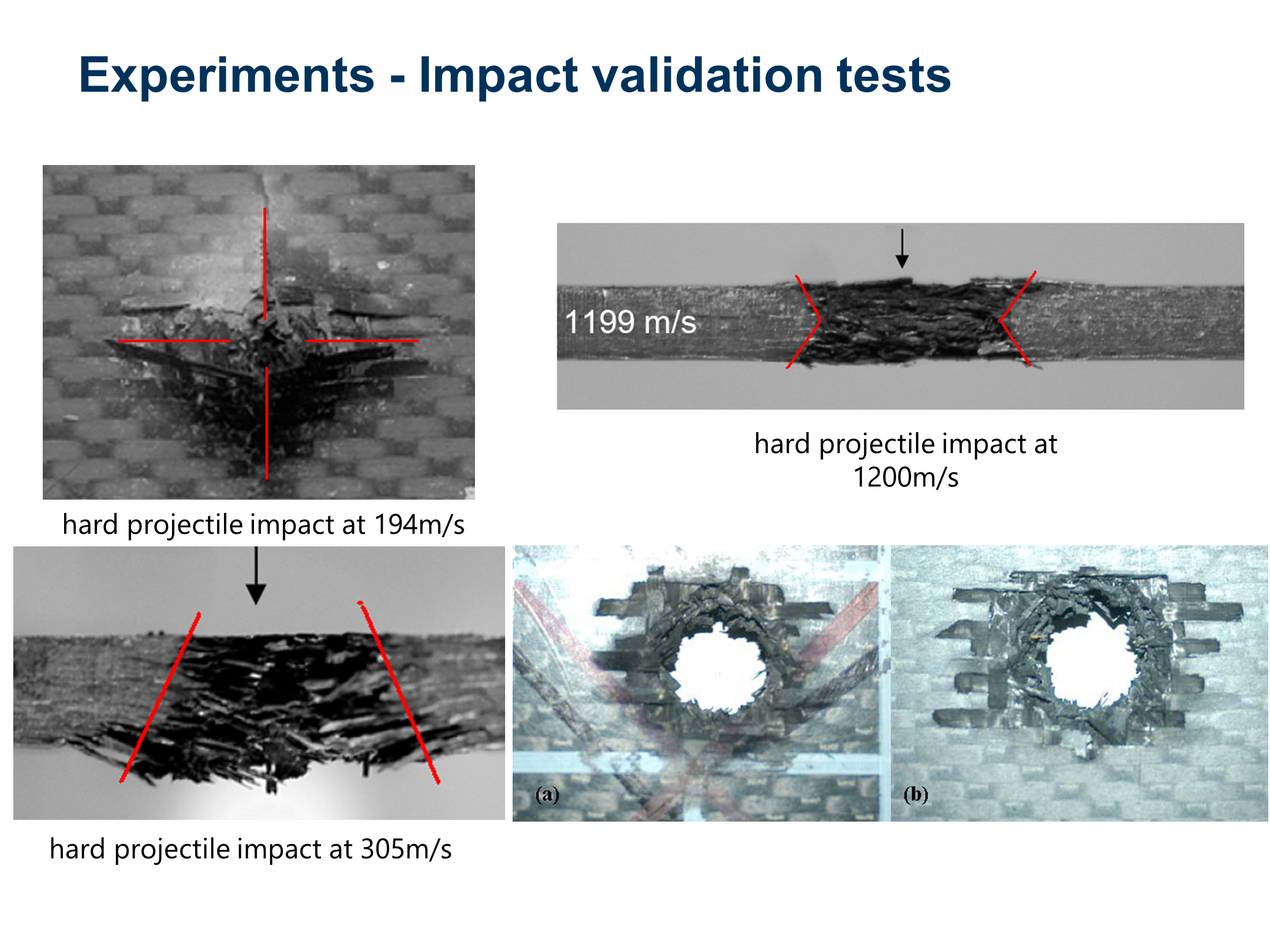
Supporting the design process
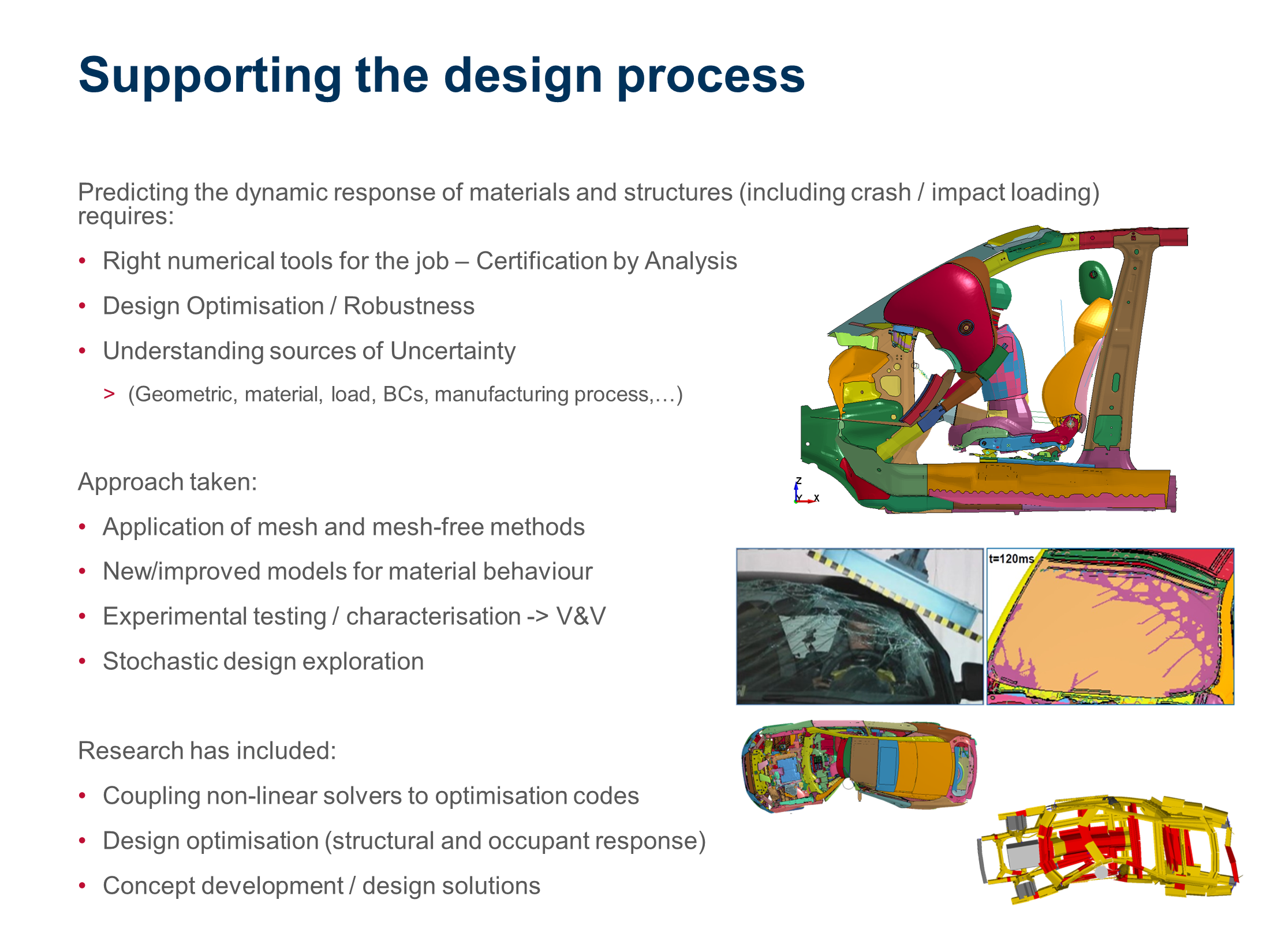
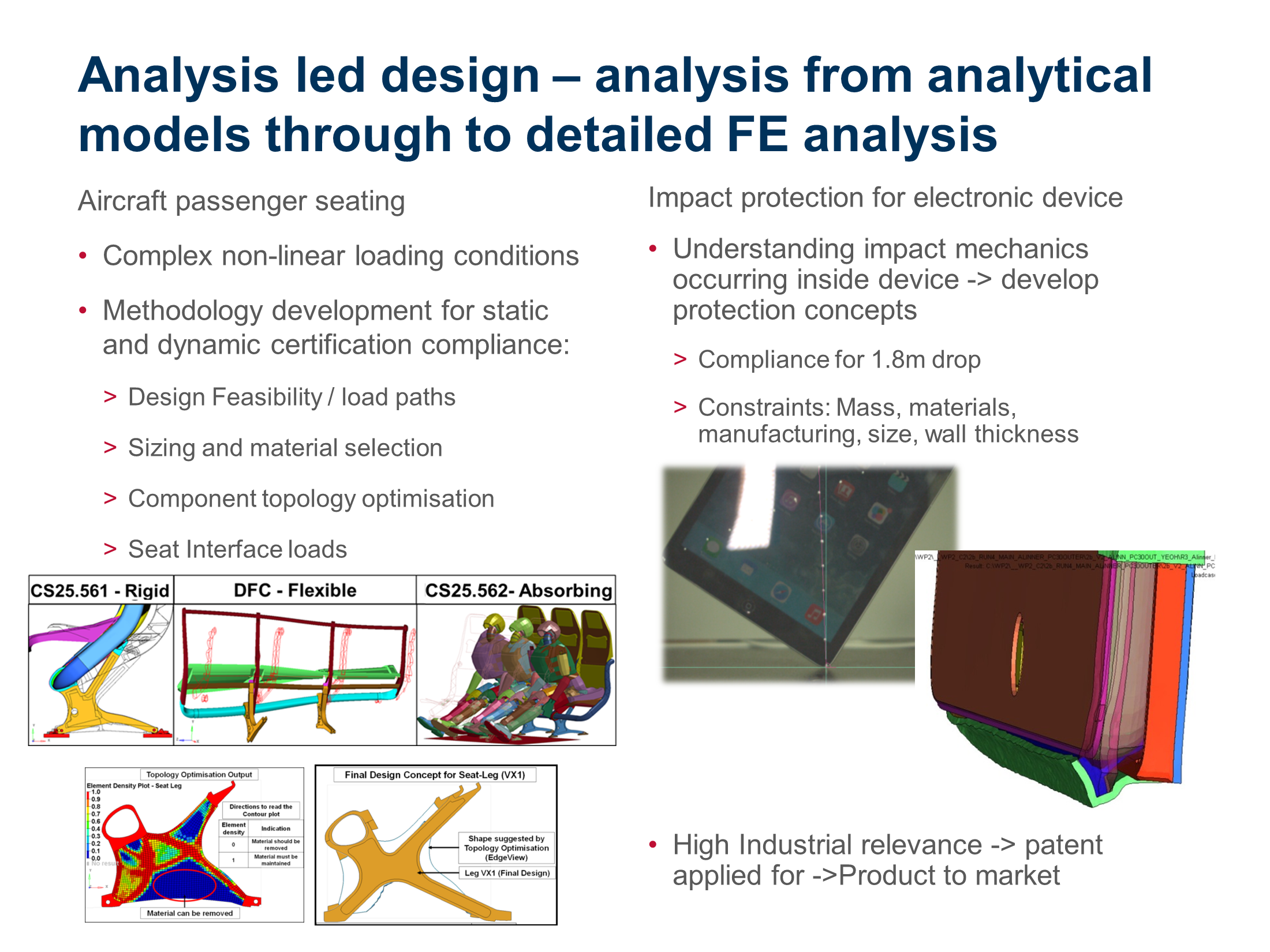
Get Help from the Experts
Contact us today to find out how we can help you